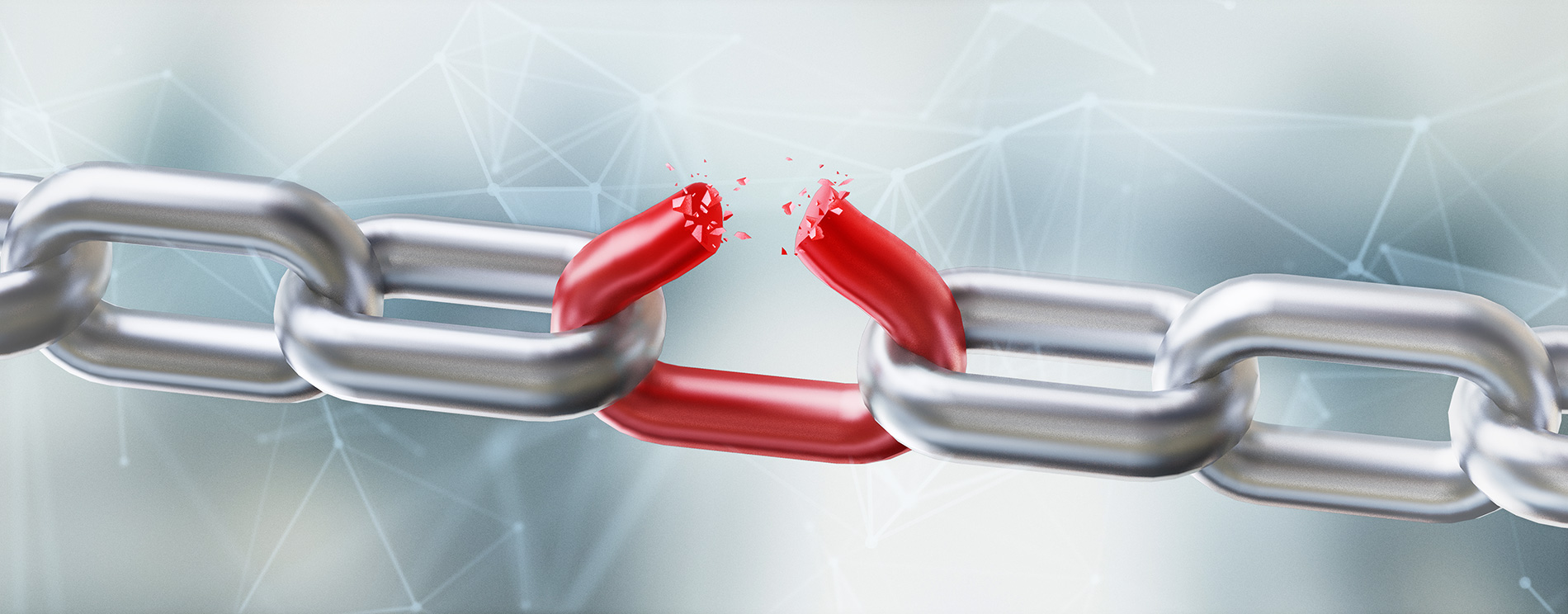
Batch job automation is a fantastic capability that saves countless hours, reduces errors, and gets the right information to the right people on time. Except when it doesn’t.
Sometimes you come into work only to learn that last night’s jobs didn’t complete on time or didn’t run at all, affecting several other related tasks—possibly affecting production on the shop floor, inventory, shipping, and even your core ERP! Now you’ve got to dig into what happened and communicate with everyone who didn’t get the updated reports they were counting on. Ouch.
Let’s take a look at the top five IBM i batch processing challenges and how to relieve the pain caused when using native or application schedulers that aren’t optimized for this platform. We’ll delve into how Robot Schedule job scheduling software can revolutionize batch process management for your organization, and give you back your peace of mind.
1. Visualizing the upstream and downstream impact of adding a job
Let’s say you need to add a job after a file import or end-of-month report is scheduled. If you don’t know how all the queued jobs relate to one another, you’re flying blind when it comes to what may happen when you insert a new task.
With native scheduler and other components built into different applications, it can be difficult to understand the overall schedule itself. Simple scheduling tools can’t give you visibility into where to put things. And for those who use CL programs, you want to know how to add new logic without breaking other processes. Especially if multiple people are involved in job scheduling, it’s hard for one person to come in and reengineer what someone else did because not everyone understands CL programming well enough to manipulate it properly.
With Robot Schedule you can access a clear job flow diagram paired with table-based job commands. If, for example, you want to add a balancing routine after the end-of-month closing, you can simply access the blueprint feature to see your current jobs and add the new ones where appropriate. Once added to the blueprint, these new tasks appear in the job flow diagram, and you can adjust any detailed processes and dependencies as necessary.
2. Receiving alerts when jobs don’t perform as they should
What happens when you don’t know a job took too long to execute? Many IBM i shops have manual checklists that operators have to maintain, often in Excel. These include the detailed steps that need to be completed as well as fields for logging start and end times and notes about abnormal completions. Others use native or application schedulers built into their ERP applications. Either way, there’s not much reporting happening behind the scenes to document SLA adherence.
With our job scheduling software for IBM i job monitors can be applied to any job. These monitors detect job overruns, underruns, and late starts. If a job is supposed to be completed by a set time and doesn’t happen, Robot Alert sends a notification.
The same can happen if a job runs too quickly, perhaps without collecting all the right data. Jobs can also get stuck in the queue, making them start late. Perhaps a minute late won’t cause problems in other jobs down the line, but what if it’s stuck for 30 minutes or an hour? You need to know what’s happening. In addition to alerts, your team can run reports to show the performance of multiple recent jobs and highlight broader trends or issues.
3. Using job and file events to trigger dependent processes
Perhaps you have a file from a PC that an IBM i process depends on. For example, there’s a 6 p.m. point-of-sale collection process that needs to detect a file on a PC at 6:30 p.m. The job has to upload the file, which triggers a batch process at 7 p.m. to update the sales data in the ERP and then create inventory and sales reports at 8 p.m.
If one of these dependent jobs doesn’t happen as anticipated, all downstream reports and data collections will be inaccurate. It all hinges on the availability of that initial file. This is important as files aren’t always available at the same time the process needs to kick off.
This is typically the case when using the native scheduler from IBM and timer jobs on a PC. Eventually the timer job on the PC won’t occur in time to keep up with what’s happening on the IBM i server. Unfortunately, you won’t know about it until the next morning when it causes some finger pointing between the IBM i team and the Windows team.
The solution is event-driven job scheduling that takes the place of timer jobs. The Robot Schedule Enterprise plug-in to Robot Schedule enables you to define a process whereby the system will monitor for files on Windows, UNIX, or Linux servers across any network drive or path that can be reached. It can then bring the file in question into IBM i. In fact, you can have an agent set up to run in the background and check for the file at a specific frequency, such as every 20 seconds. Our job scheduling software also provides access to the log for agent activity (SYSOUT, SYSERR) as well as the job log in IBM i to establish good visibility into what’s happening throughout the day.
4. Holding, skipping, or starting a job from a remote location
What happens if you need to adjust scheduled jobs or check on progress—but you’re nowhere near your computer? Maybe you’re at the store or taking a walk on the beach! As long as you have a VPN connection to your network and a smartphone or tablet, you’re all set.
Robot Schedule features a mobile, browser-based interface called Fortra Insite. This solution is free for Fortra customers and brings multiple solutions into a single dashboard for ease of administration and decision-making. When accessed via smartphone, it uses responsive design to facilitate viewing and mobile management. Maybe you got an alert that a job is stuck, and you want to know what other jobs are associated with it. Maybe you need to put one job on hold, start another immediately, or rerun a process. With Insite, you’re able to take care of immediate needs no matter where you are.
5. Calculating and automating parameter input
Did you know that parameters don’t always have to be input manually? They can be automated with dynamically calculated parameters. Our job scheduling software makes this possible by calculating processing dates, retrieving values from parameter files, and storing data for other files and passing it in. This enables you to automate tasks such as calculating the next invoice date and number, etc. The resulting date is substituted for you into the command or parameter list, such as having a report run for today’s date minus one day (i.e., yesterday). Automating parameter input is almost trivial when using this feature.
Are you ready to see Robot Schedule in action?
Learn more about how Robot Schedule workload automation software can help you take control of countless scheduled jobs.